Foundry mold Applications |
Customer Needs
In foundry applications molten metal is poured into molds to form the desired product. When the molds enter the pour area of the plant, often they are not at the proper temperature. This affects the finished part surface characteristics and may shorten the mold’s useful lifespan. Foundry molds are expensive to replace and mold longevity is a key concern. By using an Ircon Maxline 2 thermal imaging system with Image Analysis software to monitor mold temperatures going into the cooling area, end users can control cooling fan operation with better precision.
Features/Benefits to address
Product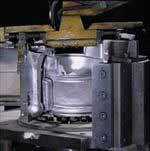
- Maxline 2 thermal imaging system with Image Analysis software
- Rugged industrial enclosure for tough environments such as foundries.
- Optional cooling enclosure and air purge for hot, dirty applications.
- Complete system comes configured from IRCON.
Application
- By looking at mold temperature prior to cooling you can more accurately predict scheduled maintenance.
- Output from Image Analysis software provides feed forward control to cooling fans.
- Wear characteristics of the mold can be determined by the temperature profile in Ircon’s Image Analysis software. Individual molds will wear differently over time. This wear can be tracked using Image Analysis software.
- Cooling time for the mold can be decreased over time once standard temperature requirements are developed.
- Less wear and tear on the cooling fan.
|